Austrian company SAG Motion Technology approached Impact to assist with the fuel tank development of their rotolined aluminium containers for the storage of Adblue®, which is an additive used to reduce the NOx emissions from fuel. The lining is intended to protect the aluminium from attack and thus prevent contamination to the fuel system. It is important that the polyethylene forms an integral lining and that debonding does not occur. The interaction between the Adblue® and the polymer is unknown and has the potential to diffuse through the polymer and affect its adhesion to the aluminium.
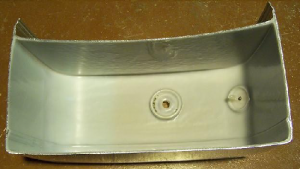
Fuel Tank development
Three rotolining grades of polyethylene were evaluated using both small-scale laboratory tests and final product tests. The initial screening of the materials involved compatibility assessment in Adblue® to see whether there were any concerns regarding absorption, degradation or stress-cracking of the polymer.
The second stage of the work established laboratory methods for simulating the rotolining process on a laboratory scale and measuring the adhesive performance of the materials to aluminium. This allowed the influence of process variables to be explored followed by detailed study of the effect of exposure of the lined aluminium to Adblue® at different temperatures.
Following the laboratory work, the best material was selected and prototype rotolining trials were performed using 120 litre vessels. The products were assessed in terms of their quality, in particular the integrity at the filler neck region, and thorough evaluation of the adhesion at different locations was performed after exposure to Adblue® at a range of temperatures.
This systematic approach led to high confidence in material selection based on laboratory scale work ratified by prototype evaluation. Further work is in progress to commercialise the product.
Contact us if you are interested in Fuel Tank development.
To keep up-to-date with Impact Solutions, follow us on Twitter, LinkedIn and Facebook.