flow properties
plastic rheology and melt flow rate (MFR)
Melt Flow Rate (MFR)
Melt flow rate (MFR), while a simple straight forward test is massively valuable in plastic testing. It is universally used across the plastic processing industry to measure a range of properties derived from one simple calculation.
The melt flow rate (or melt flow index) can reveal the likely density of the material, its source (in the case of plastic recycling) and indicate other properties such as tensile and impact performance.
The test is performed using a melt flow machine.
The melt flow machine consists of a heated block, which can be heated to different temperatures. Through this block is a column where granulated, or pelletised plastic pellets can be melted. A capillary die head of 2.0866mm in diameter (and 8mm in length) is located at the base of this heated column. A piston is then used to force the molten polymer through the die head. The piston is loaded with a weight, with the weight differing depending on the polymer used. The set up is shown in the diagram, right:
The melt flow rate testing is carried out usually to either ISO 1133 or ASTM D1238. Different temperatures are used for the melt flow rate testing depending on the polymer with HDPE processed at 190C and PP processed at 230C. The weight can also change depending on the polymer (PP usually uses a 2.16kg weight) while PE can use either a 2.16kg or 5kg weight depending on the expected polymer melt flow rate. Extrusion grade or fractional melt PE can be tested using a 5kg weight for greater accuracy.
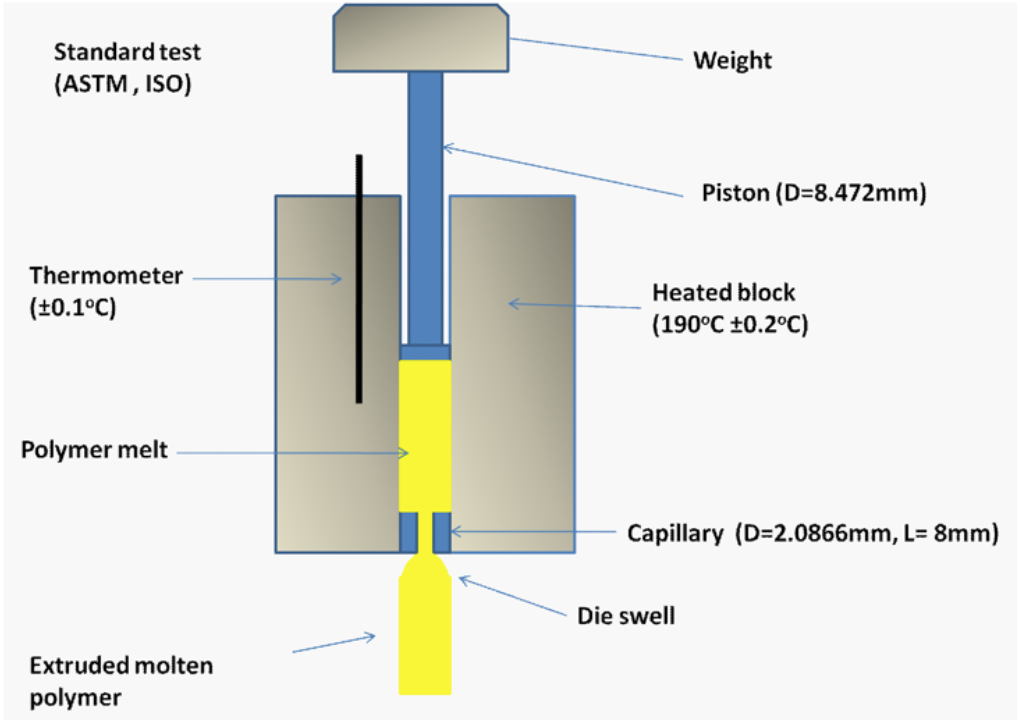
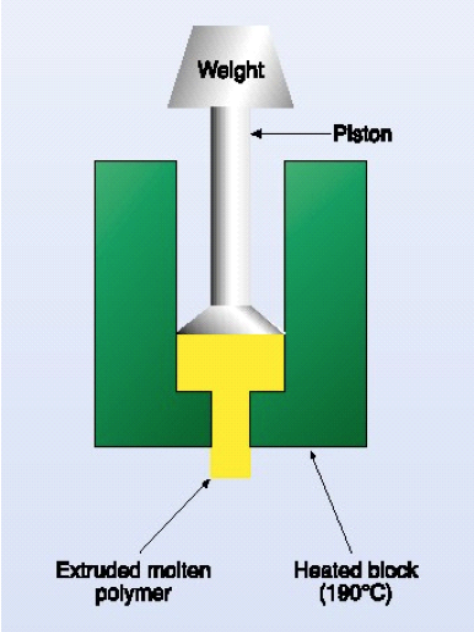
Datasheets
If processing high molecular weight polymers a load of 21.6kg can be used and this figure is usually then expressed as a high load melt index (HLMI). Whatever the temperature or load used, the data sheet should be very careful to mention, otherwise, the figure obtained is meaningless. A typical recycled PP for example could be represented on a datasheet as:
20 g/10min 230C @ 2.16kg
The value is expressed as g/10min. This is because the melt flow rate test is performed by cutting samples at regular intervals from the end of the die head. These samples are cooled and then weighed in grams. The time is measured for each ‘cut’.
An average of the weights is then taken, with the result multiplied by 600 (for 600 seconds, or 10 mins) and then divided by the ‘cut’ time. For example, if cuts are taken every 30 seconds, and the average weight of the cuts was 1g, then the calculation would be;
1g x 600 / 30 = 20 g/10min 230C @ 2.16kg
While a simple test, melt flow rate is such an important parameter on a datasheet it is important it is measured correctly. Impact run the test under UKAS ISO 17025 accreditation and have more than 40 years of experience in regular melt flow rate testing, making us a key UK expert in melt flow rate testing and further rheology consultancy. You can contact us on info@impact-solutions.co.uk or on 01324 489182.