The extremely worrying outcome of a recent study that waste plastics floating in the world’s oceans have entered into the oceans food cycle (Andrés Cózar et al. PNAS, June 2014), is just another wake-up call to turn our attention to the recycled plastic products. Plastics, which are made of hydrocarbons, are slowly biodegradable materials. Due to this non-biodegradable property the waste management of the plastics has become a significant issue. Although nowadays almost all plastics are possible to be recycled, economical, technical and handling issues limit the full recycling of these materials.
A series of techniques for dealing with the post-consumer and industrial plastics have been developed, such as incineration, pyrolysis and reprocessing-reuse. Incineration and pyrolysis, which are related to the production of energy from the waste plastics suffer from environmental pollution issues as well as low value to production cost ratio. Reprocessing of waste plastic materials for reuse may reduce carbon footprint when compared to the other techniques and compared to the manufacturing/processing of virgin plastics. The waste plastics are usually being recycled in the form of blends i.e. melting the mixed waste plastics and produce new plastic materials. Given that polyethylene (PE) and polypropylene (PP) are the most commonly used polymers in our daily lives and in the industry, mixed waste PE and PP (Fig.1) are the common building blocks of the new recycled plastic materials.
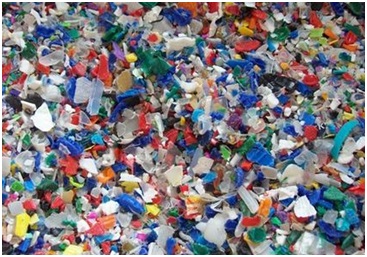
Figure 1. PE and PP waste plastics for recycling
However, products made from mixed recycled plastics with random volume ratios of PE and PP, suffer from non-specific weathering, thermal, mechanical and ageing properties, making them difficult to handle and finally increasing their production cost for the moulding factories. As a result, determining the concentration of each polymer in a mixed recycled plastic is of paramount importance and would contribute to the production of more efficient and low-cost recycled materials. Among other characterization techniques, the use of differential scanning calorimetry (DSC) has been proved an effective, reliable and fast method for the identification and quantification of polymers such as PE and PP in waste and recycled plastics.
DSC is a thermal analysis technique measuring how the material’s heat capacity is changed by temperature. During testing, a sample of known mass is heated and/or cooled and the changes in its heat capacity are tracked as changes in the heat flow. This will enable the detection of transitions such as melt, crystallization, glass transition etc. Plastics, which are mainly consisted of semi-crystalline polymers yield characteristic-unique melting, crystallization and glass transition peaks in a typical DSC heat flux versus temperature or time curve. The area below the melting, which is defined as the enthalpy of melting ΔΗ, is primarily used to determine the purity and the degree of crystallinity of the materials. In the particular case of polymer blends, the melting temperatures do not change with the percentage of the polymers in the mixed plastic sample. In addition, the ΔΗ varies linearly with the percentage of the polymers in the blend. These would ultimately turn the ΔΗ into an excellent tool for quantifying the polymers in the mixture.
In order to justify the great advantages of the DSC on the quantitative analysis of plastics, in Impact Solutions, where we are equipped with a state-of-the-art DSC Polyma 214 from Netzsch, we prepared and characterized a series of high-density polyethylene (HDPE): PP plastics. Plastics were prepared in our laboratories from virgin resins of HDPE and PP, mixed in the Brabender to produce volume ratios of HDPE: PP 100:0, 70:30, 50:50, 30:70 and 0:100. Samples of the mixed HDPE: PP plastics were placed in the advanced Concavus Netzsch pans. Subsequently, the pans with the samples were placed in the DSC for analysis. The testing parameters included heating, cooling and heating from -30 oC to 240 oC with heating rate 20.0K/min and nitrogen gas flow 40.0 ml/min. Upon testing, the transition peaks of the samples were identified using the advanced Proteus software focusing on the melting areas.
Figure 2, presents the melting peaks in the heat flow versus temperature DSC curves of the HDPE: PP samples with various volume ratios. The HDPE: PP 100:0 and 0:100 samples showed one melting peak at approximately 136 oC and 163 oC, which compare well with the characteristic melting temperatures (Tm) of the HDPE and PP, accordingly. The HDPE: PP 70:30, 50:50 and 30:70 samples showed two melting peaks, which correspond to the HDPE and PP parts in the blend. The enthalpies (ΔΗ) below the melting peaks and the height of the melting peaks (showed with arrows in Fig.2) varied with the percentage of the polymers in the blend.
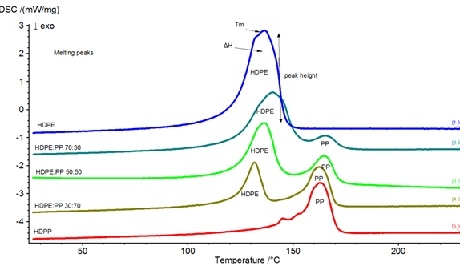
Figure 2. DSC melting temperature peaks of the HDPE:PP 100:0, 70:30, 50:50, 30:70 and 0:100 mixed plastics. The areas below the melting peaks correspond to the melting enthalpies of each polymer in the plastic.
Figures 3a and b present the plots of the melting enthalpies versus the %HDPE and PP, accordingly. Analysis of the melting enthalpies revealed that the ΔΗ increases linearly (linear factors, R2>0.9) with the concentration of the polymers in the plastics. Figures 3c and d show the relation between the melting peak height and the concentration of the polymers. The height of the melting peaks increases with the %HDPE/%PP exhibiting a much linear behaviour (R2>0.97) compared with the ΔΗ plots.
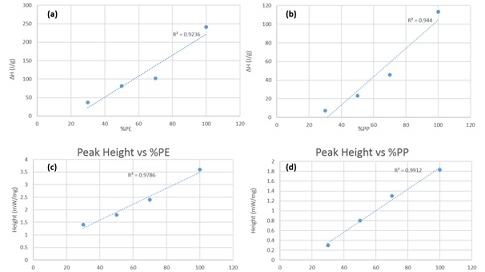
Figure 3. a-b Melting enthalpy versus %HDPE and %PP; c-d Melting peak height versus %HDPE and %PP.
The linear behaviour of the ΔH and melting peak heights versus polymer percentage plots offers an unprecedented technique for quantifying the polymer blends in the recycled plastics. The melting peak in particular exhibited a nearly perfect linear increase with the increase of the polymer parts. The use of advanced and state-of-the-art DSC systems such as the Polyma 214 from Netzsch combined with the SMART mode and Proteus analysis software, turn the total plastic identification into a reliable, reproducible, fast and low-cost process.
Except for qualitative and quantitative analysis of virgin polymers and plastics, in Impact’s laboratories we are also using the DSC Polyma 214 on a daily basis to obtain the thermal properties of the polymers for use in moulding and semi-positive moulding processes, as well as for performing oxidation induction time and oxidation onset temperature according to the national and international standards such as ASTM D3895 (polyethylene), DIN EN 728 (plastic pipelines) or ISO 11357-6 (plastics).
For further information regarding Impact Solutions capabilities on thermal analysis please contact us today!