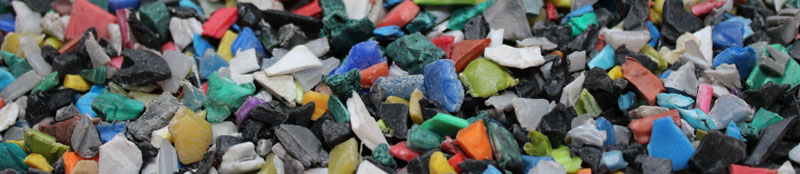
DSC analysis of recycled plastic
Differential scanning calligraphy (DSC) is a key technique used to determine the purity of polymers. DSC works by heating a crucible of polymer material through a temperature range and measuring the weight change at each temperature point. As different plastics melt at different temperatures a curve can be built up showing the energy required to melt at a given point. This allows us to work out exactly how much of each type of plastic is in a mix.
It is also a great technique for showing just how effective BOSS can be at seperating mixed polyolefins.
Below we have a real-world example. The input material on the left is from mixed rigids which have been handpicked to produce what the recycler was hoping was a pure HDPE steam. The large peak at around 125C is indeed where you would see PE. However, what the recycler wouldn’t want to see if the smaller peak at around 160C which is indicative of PP. The PP mixed in the PE causes a problem for manufacturers as the two plastics are not compatible and cause a weaker product to be made. The presence of PP also causes a higher melt flow, and as the majority of recycled HDPE is used in extrusion applications this makes the plastic too runny.
DSC of PE before BOSS

DSC of PE after BOSS

Next, we have a Polypropylene rich material. The input material on the left has been taken from PP produced off a Redwave optical plant. The strong peak at 160C shows a large amount of PP content, however, the peak we do not want to see is at 125C. This is common with optically sorted material, as the sorters are designed to remove contamination. They ‘eject’, usually with compressed air, the identified plastic into separate buckets, but will also take some of the non-target material with it.
DSC of PP before BOSS

DSC of PP after BOSS

On the right we have the same PP material after BOSS. As you can see there is now just one large peak and the earlier peak has disappeared entirely. The onset of the peak is slightly earlier than expected, and this suggests there is still a tiny quantity of PE in the mix, but it is now overwhelmingly a PP material. This produces a huge uplift in value, as the Melt Flow rates are improved and the material can be used in higher grade applications.
Impact have produced a range of business plans for how BOSS can be used to improve the quality of your mixed polyolefin rich recycled feedstocks. We can work with you from baled product, right through to high quality regrind, or introduce you to a business model to take the extensive range of mixed polyolefin regrind in the market and turn it into high quality feedstocks. Contact the recycling team now on 01324 489 182 or email info@impact-solutions.co.uk for more information.